Providing outstanding technical services to our customers is an important concern to us, and in fact one of our core businesses. Often we are challenged by our customers to increase the production rate or improve product quality with minimal or no investment. Our services range from technical support for the production of all carbon materials, to plant audits and process optimizations. In our technology center we conduct pilot or bench scale trials and any kind of laboratory analysis with detailed evaluations. We analyze shipment samples according to standardized ISO methods for certification of the specifications or for arbitration purposes.
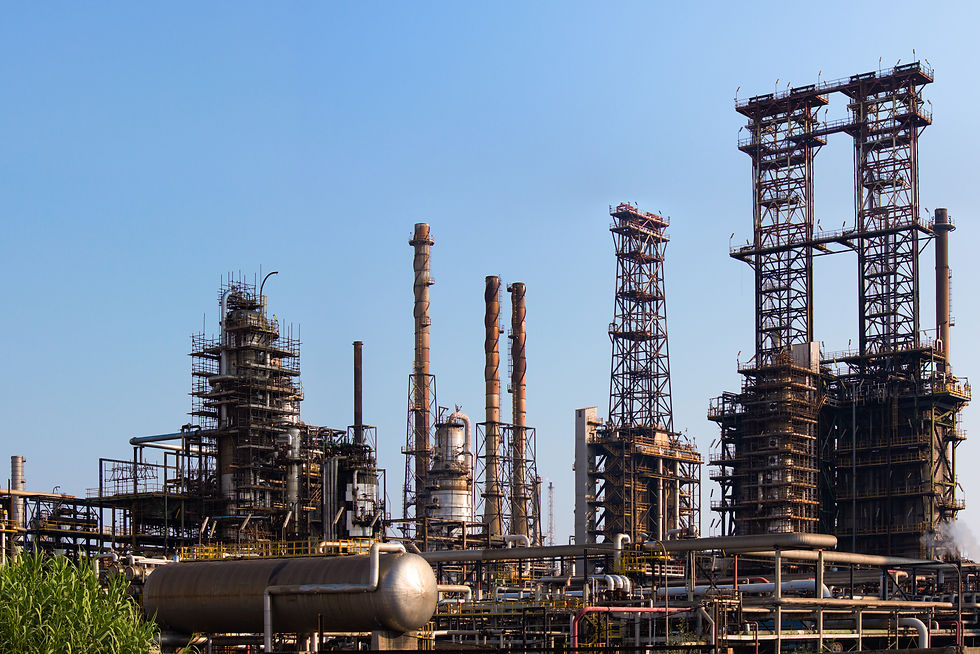
Anode, Cathode and Electrode Production Plants
R&D Carbon has a vast experience in technical plant audits. We perform a systematic plant assessment in an independent, purely technical manner. We focus on finding areas with potential for improvement to reduce the aluminium production cost as the ultimate goal.
We apply a very systematic methodology by following the material stream from the raw materials intake all the way to the pot rooms and the butts recycling station. Every relevant processing step is investigated by sampling the product and analyzing its important properties. We then compare the test results with our extensive database of worldwide typical figures for level and consistency as well as benchmark values.
All observations, test results, findings and recommendations are compiled in a comprehensive report. This audit report is presented and discussed in detail with all key people of the audited plant and often serves the plant as a reference and guideline for many years to come.
With this approach we can provide an assessment with recommendations that are based on sound facts and figures. We are capable to define target figures and the required measures. We give recommendations for improvements that can be realized with no or little capital expenditure. If investment is needed, we provide the plant manager with all relevant input figures to create a sound and realistic business case.
Often, the plant audit is the starting point for the commencement of a technical consulting agreement to assist the plant during the implementation of the recommendations. Alternatively, the plant audit may be directly followed by a dynamic process optimization of the paste plant (DPO) and/or the bake furnace (FPO).
Technical assessment of the carbon production and performance from an independent institution with vast experience in this field
Comparison of product quality (level and consistency) with worldwide typical figures and benchmark
Identification of production areas with potential for improvement to minimize smelter cost
Recommendations for instant cost savings or gains in product quality
Comprehensive audit report as a reference and guideline for future decisions about plant modifications and/or optimization trials
Your benefit
Anode Bake Furnace
" With furnace audits and optimizations, we help you to cope with today's aggravated boundary conditions such as increased cost pressure, stricter emissions regulations and deteriorated raw material quality. "
Peter Sulger
Process, Development and Data Analysis Vice President
Anodes are a vital material for aluminum smelters, and anode baking is a crucial step in making them. Every modern smelter is focused on maximizing its profit by constantly optimizing its productivity at minimal capital and operating cost. Higher amperage and longer anode setting cycle are postulated which require baked anodes of superior quality and consistency. Parallel to that, local authorities define more stringent environmental restrictions for plant emissions. With today’s trend of decreasing anode raw material quality, this is a major challenge for the carbon plant manager to cope with all these requirements.
It is part of our core business to give active assistance to detect deficiencies and potential for improvement. All services are provided regardless of any applied technology and control system. In the over 30-year old history of R&D Carbon, we have accomplished major improvements in plants all over the world. In the straightforward approach, a furnace audit is conducted first to evaluate the potential for improvements. Then systematic optimization steps with defined targets are performed.
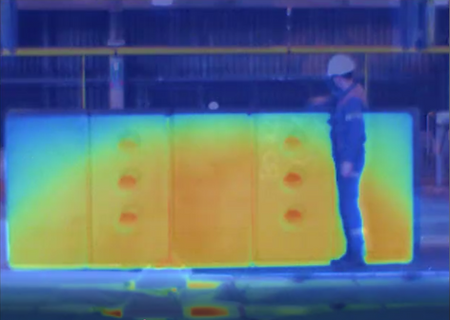

Our worldwide activities on furnaces of any design and any firing control system allow us improving substantially the furnace operation and the anode quality. As a consequence R&D Carbon contributes considerably to reduce the overall metal production costs and to lower capital investment for production plants.
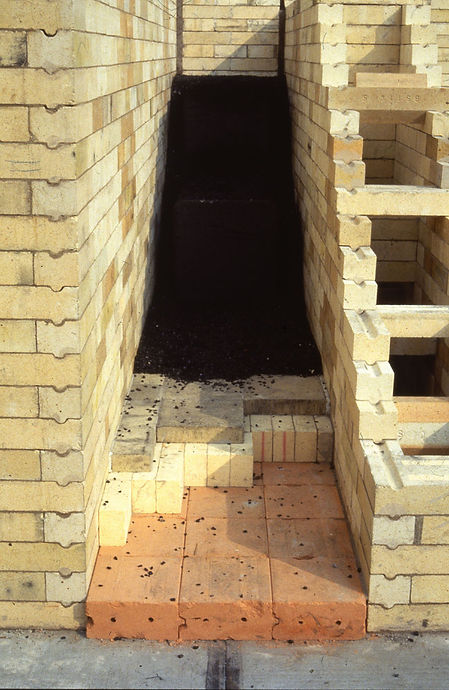
Bake furnace operation and achieved anode quality are strongly interlinked with the furnace design. Therefore, in recent years RDC has conducted numerous studies and analyzes on design and dimensioning of anode bake furnaces. Always with the aim of optimizing the furnace design with respect to the cost impact, achieving the highest anode quality, reducing emissions and achieving best-operating behavior.
Benchmark Anode
" Benchmark anodes are a key factor for the reduction of your aluminium smelting cost, we are ready to help you anytime."
Matthieu Arlettaz
CEO
Technical assistance to worldwide active trading companies and smelters is an important way to improve anode and cathode qualities supplied to the Aluminium Industry. The "Swiss Made in China Quality Model" together with our American partner Aminco Resources LLC is an example of successful ten years cooperation with more than three million tons of anodes produced and exported to customers around the globe. R&D Carbon is able to help worldwide clients to produce benchmark anodes, for reducing the aluminium smelting cost.
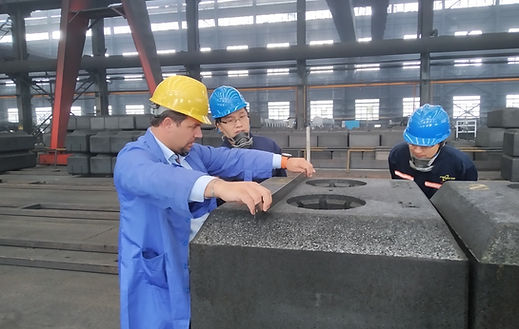